Why Your Conveyor Setup Isn’t Complete Without This
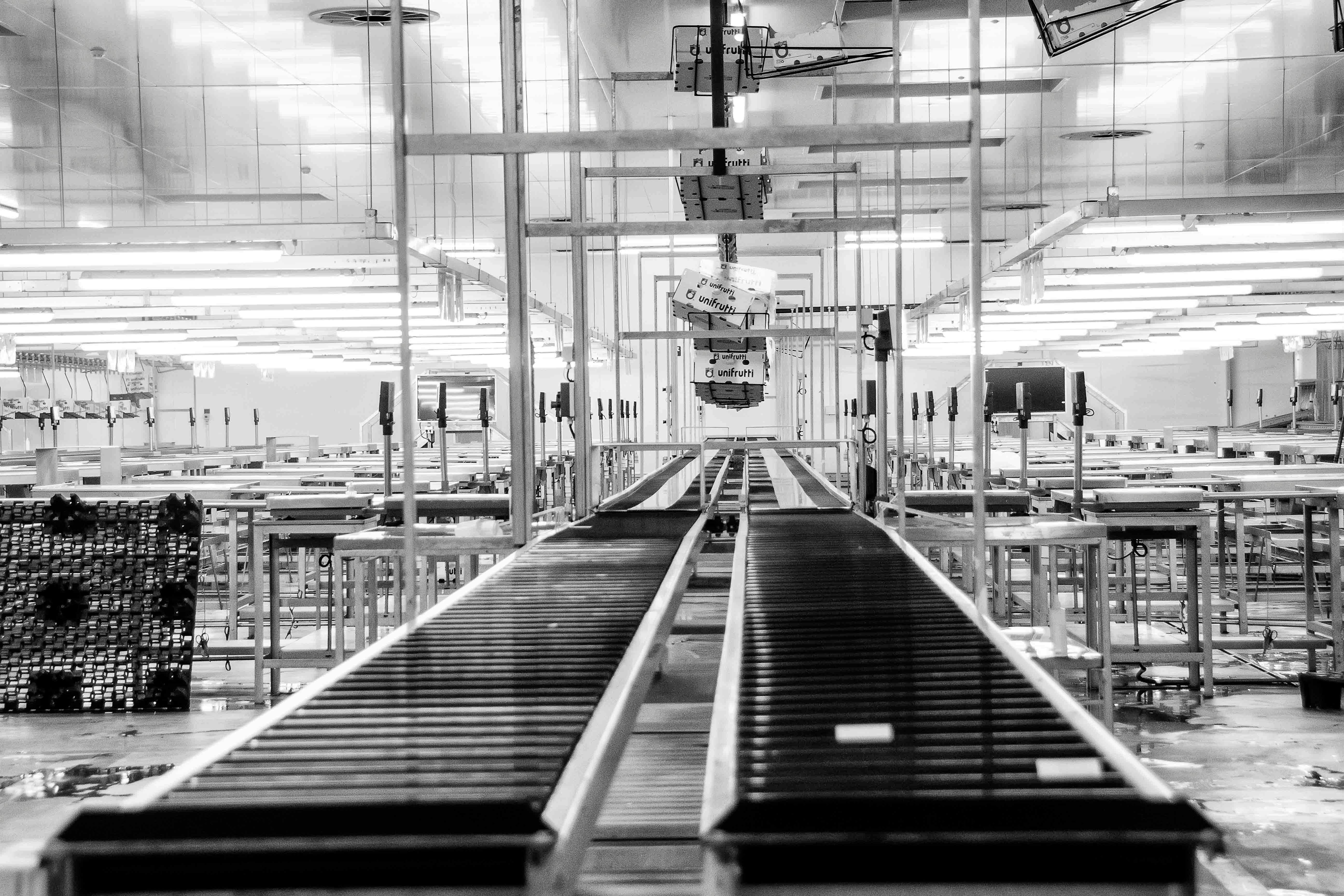
What’s the point of investing in a high-performance conveyor system if it’s constantly breaking down, costing time and money in maintenance and repairs?
It’s a frustrating cycle. And the most surprising part? In many cases, the core issue comes down to one missing piece — the impact bed.
The Problem No One Talks About
A lot of attention goes into things like belt speed, motor power, and tracking systems. But when it comes to the loading zone — the spot where tonnes of material slam onto the belt — many setups fall short. Hard. This is where things often go wrong.
Without proper support at the load point, you’re left with:
- Belt damage – repeated impact leads to cracks, gouges, and premature wear.
- Material spillage – gaps in support cause the belt to flex, letting fines escape.
- Roller failure – traditional rollers can’t take the constant impact and end up failing fast.
- Increased maintenance – more breakdowns mean more downtime and higher costs.
If your system is still using standard idlers in high-impact areas, you’re likely facing at least one of these issues. Probably more.
What Exactly Is an Impact Bed?
Impact beds are specially designed support structures placed under the belt at the loading point. Unlike standard rollers, it offers a continuous, flat surface that absorbs shock, distributes weight, and protects the belt from heavy, abrasive loads.
It’s built tough. Think thick, layered impact bars made with rubber and low-friction surfaces that reduce drag while resisting wear. And because it’s one solid surface instead of individual rollers, it doesn’t leave unsupported gaps that can cause belt sag or spillage.
Why Standard Rollers Just Don’t Cut It
Rollers have their place — but not here. The load zone is brutal. Imagine tonnes of rock, ore, or other material dropping from a height. Traditional rollers simply aren't built to handle that repeated punishment. They bend. They snap. They seize up. And when they do, the belt suffers too.
You might already be seeing the signs:
- Belt edges curling
- Spilled product piling up at the tail
- High maintenance around your loading area
All of this adds up to lost time and increased costs, both of which can be avoided.
What an Impact Bed Actually Does for Your System
Here’s where things get interesting. An impact bed doesn’t just prevent problems. It actively improves the performance of your entire conveyor.
1. Extends Belt Life
By absorbing the energy from falling material, an impact bed protects the belt from repeated high-pressure strikes. This reduces the risk of splits and punctures, especially at the edges, which are often the weakest points.
Over time, this means far fewer repairs and replacements. And belts aren’t cheap.
2. Reduces Material Loss
With rollers, there's flex between each point of contact. That slight movement creates gaps where fine materials can escape. Multiply that by every hour of every shift, and you’re losing serious product.
An impact bed removes that flex, sealing the belt edge against the skirting and keeping material where it belongs — on the belt.
3. Cuts Down On Maintenance
Rollers wear out fast under impact. When they do, they can seize up, gouge the belt, and create messes that need cleaning daily. Constant roller replacements also burn through budgets and downtime.
An impact bed, on the other hand, has no moving parts in the load zone. It’s durable, stable, and built to last.
4. Improves Safety
Less spillage and fewer failures mean a cleaner, safer work environment. Workers aren’t spending hours under the belt replacing failed rollers or cleaning up material, which lowers the risk of injury.
That’s more than just a nice bonus — it can have real implications for site compliance and incident reporting.
5. Provides Smoother Transitions
The load zone should be a smooth handover, not a rough impact. A well-designed impact bed creates a gentle transition for material, protecting both the belt and structure beneath it.
This smoother loading action also helps maintain consistent belt tracking, avoiding lateral shifts that can lead to misalignment and further wear.
What to Look For If You're Adding One
Not all impact beds are equal. If you’re considering upgrading, it’s worth checking that your setup includes:
- Modular frame design – easier installation and maintenance access
- High-friction-resistant bars – to minimise drag while supporting the belt
- Proper sizing for belt width and drop height – impact beds must be matched to your system specs
- Edge sealing compatibility – to help contain material and reduce spillage
Time to Rethink Your Load Zone?
It’s easy to overlook what’s happening at the loading point. It’s a small section of the conveyor, after all. But it’s where some of the biggest stresses happen.
If your conveyor setup is struggling with spillage, belt damage, or ongoing maintenance headaches, don’t ignore the role of impact protection.
An impact bed is a practical upgrade that protects your investment, reduces headaches, and boosts performance.
Get the load zone right, and the rest of your conveyor just runs better. Simple as that.